Plastic Injection Molding China: Leading the Future of Manufacturing
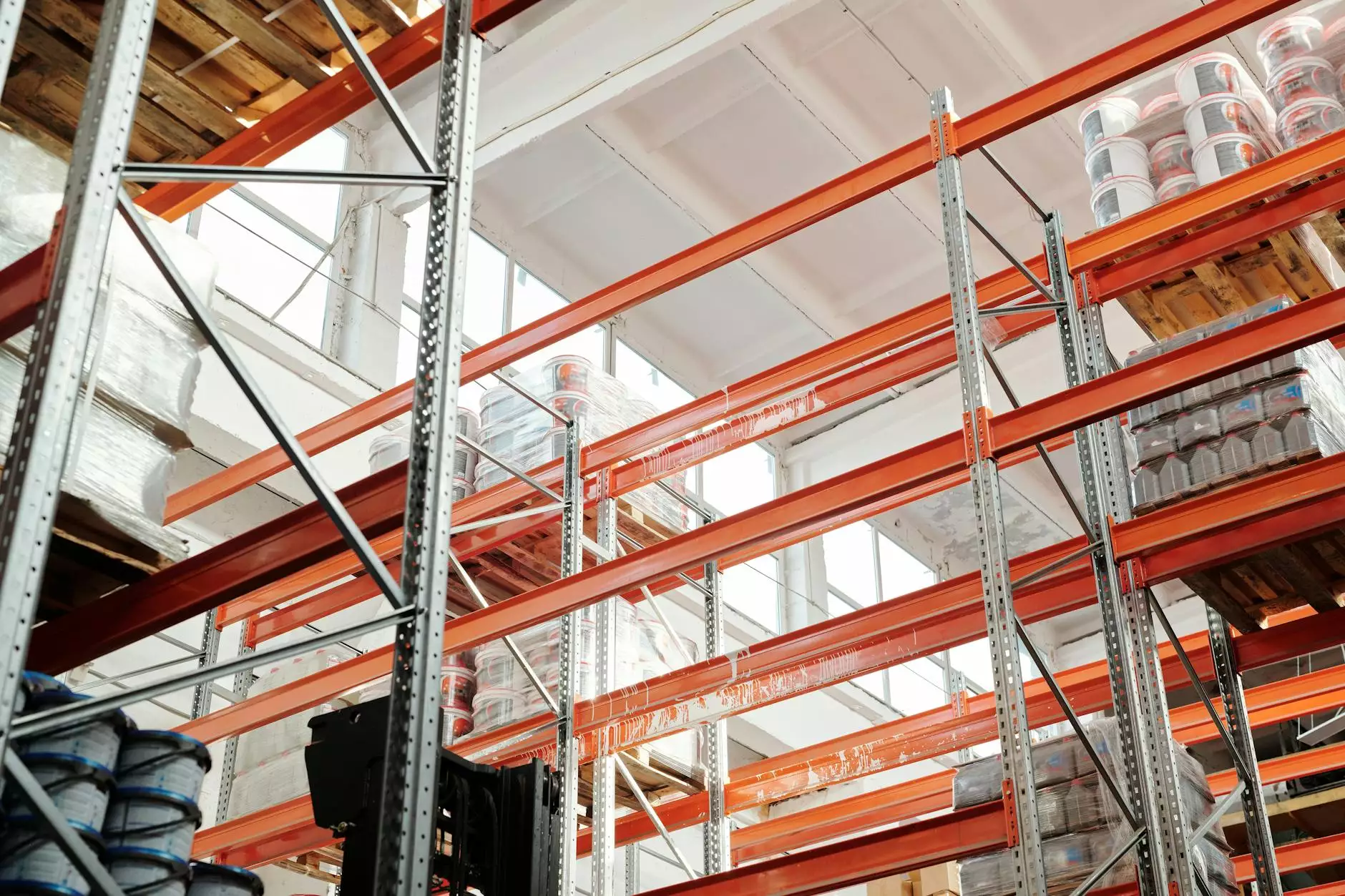
In today’s fast-paced business environment, the demand for high-quality, cost-effective manufacturing processes is ever-growing. One technique that has revolutionized the manufacturing industry is plastic injection molding. With China emerging as a global powerhouse in this sector, understanding the intricacies of plastic injection molding in China can greatly benefit businesses worldwide. This article delves into the advantages, processes, and future prospects of plastic injection molding in China, positioning it as the ideal choice for manufacturers.
Understanding Plastic Injection Molding
Plastic injection molding is a manufacturing process whereby molten plastic is injected into a mold cavity, allowing it to cool and solidify into the desired shape. This method is favored for its ability to produce high volumes of identical parts with incredible precision. The process involves a few key steps:
- Material Selection: The first step involves choosing the right type of plastic resin based on the requirements of the end-use application.
- Mold Design: Engineers design a mold that meets the specifications of the product, taking into account factors like cooling time and ease of part removal.
- Injection Process: The plastic resin is heated until it becomes molten and is then injected into the mold under high pressure.
- Cooling: The molded plastic is cooled, allowing it to solidify into its final form.
- Part Removal: Once cooled, the mold opens, and the finished part is ejected from the mold.
The Advantages of Manufacturing in China
When it comes to plastic injection molding, manufacturing in China offers numerous advantages that cannot be overlooked:
1. Cost-Effectiveness
China is renowned for its affordable manufacturing capabilities. The lower labor costs combined with efficient production processes enable businesses to save significantly on overheads, making plastic injection molding in China a highly attractive option. By leveraging these cost advantages, companies can enhance their profit margins while providing competitive pricing for their products.
2. Skilled Labor Force
China boasts a vast pool of skilled labor in the plastics manufacturing sector. Engineers and technicians trained in advanced molding technologies ensure that manufacturers produce top-quality products. The experience and expertise of these professionals mean that companies can rely on high standards of workmanship.
3. Advanced Technology
As manufacturing technology continues to evolve, China remains at the forefront of these innovations. The country invests heavily in cutting-edge machinery and technology for plastic injection molding, ensuring high efficiency, precision, and repeatability in production. This modern approach translates to quality products with minimal defects.
4. Rapid Production Speed
The ability to produce components quickly is essential in today’s market. China’s robust manufacturing infrastructure, combined with project management efficiencies, allows businesses to bring their products to market faster—crucial for maintaining a competitive edge.
5. Comprehensive Supply Chain
China has developed a complete supply chain for plastic injection molding, from raw materials to finished products. Local suppliers of plastic resins and components lower transportation costs and lead times, further streamlining the production process. This integrated supply chain is a significant advantage for manufacturers looking to optimize their operations.
Applications of Plastic Injection Molding in Various Industries
Plastic injection molding is used in a myriad of industries, thanks to its versatility and efficiency. Some notable applications include:
- Automotive Industry: Plastic components are widely used in vehicles, including bumpers, dashboards, and interior parts.
- Consumer Electronics: Injection molding produces casings and structural components for smartphones, tablets, and other electronic devices.
- Medical Devices: Precision and reliability in manufacturing are critical in the medical field, making injection molded parts ideal for syringes, surgical instruments, and more.
- Packaging: Customizable molds allow for creating unique package shapes and sizes that cater to various products.
- Household Goods: Everyday items like kitchenware, storage containers, and toys are often produced through injection molding.
The Future of Plastic Injection Molding in China
The future of plastic injection molding in China looks promising, with various trends shaping its landscape:
1. Sustainability Initiatives
With the increasing focus on sustainability, manufacturers are incorporating eco-friendly practices. This includes using recycled plastics and optimizing energy consumption during the molding process. Companies that adopt sustainable practices are likely to attract more customers who value environmental responsibility.
2. Automation and Smart Manufacturing
The integration of automation and smart technology in injection molding is on the rise. From robotics that perform repetitive tasks to IoT systems that track production efficiency, these advancements aim to reduce costs while enhancing productivity. Embracing these technologies will position businesses ahead of their competitors.
3. Customization and Rapid Prototyping
As consumer preferences lean toward personalized products, there is a growing demand for custom molds and rapid prototyping. Chinese manufacturers are responding by offering flexibility in production runs and expedited prototyping services, allowing businesses to adapt quickly to market needs.
4. Global Collaboration
China's role as a manufacturing hub means that businesses across the globe can collaborate more easily. Whether through partnerships or outsourcing, companies can tap into China's expertise, resources, and technological advancements in plastic injection molding.
Choosing the Right Manufacturer
Partnering with a reliable manufacturer for plastic injection molding is crucial to ensuring quality. Here are key factors to consider:
1. Experience and Specialization
Select a manufacturer with a proven track record in plastic injection molding. Evaluate their experience specific to your industry to ensure they understand your quality standards and requirements.
2. Quality Assurance Protocols
Inquire about the quality assurance measures in place. A reputable manufacturer should have stringent quality control processes to minimize defects and ensure compliance with international standards.
3. Communication and Support
Transparent communication is vital throughout the production process. Ensure the manufacturer provides comprehensive support, from initial design consultations to after-sales service.
4. Facility Tour
Whenever possible, visit the manufacturing facility. This allows you to assess their capabilities and see their operations firsthand, ensuring they meet your expectations.
Conclusion
In conclusion, plastic injection molding in China stands as a cornerstone of modern manufacturing, offering unparalleled advantages in cost, speed, and technology. As businesses increasingly rely on high-quality, efficient production methods to stay competitive in the global market, the benefits of partnering with Chinese manufacturers for injection molding cannot be overstated. By embracing the innovations and capabilities that China provides, companies are poised to achieve greater success while meeting the ever-evolving demands of consumers.
As the industry continues to evolve, staying informed and choosing the right partners will be essential in leveraging the full potential of plastic injection molding to propel your business forward.
plastic injection molding china