The Precision of CNC Machines in Metal Fabrication
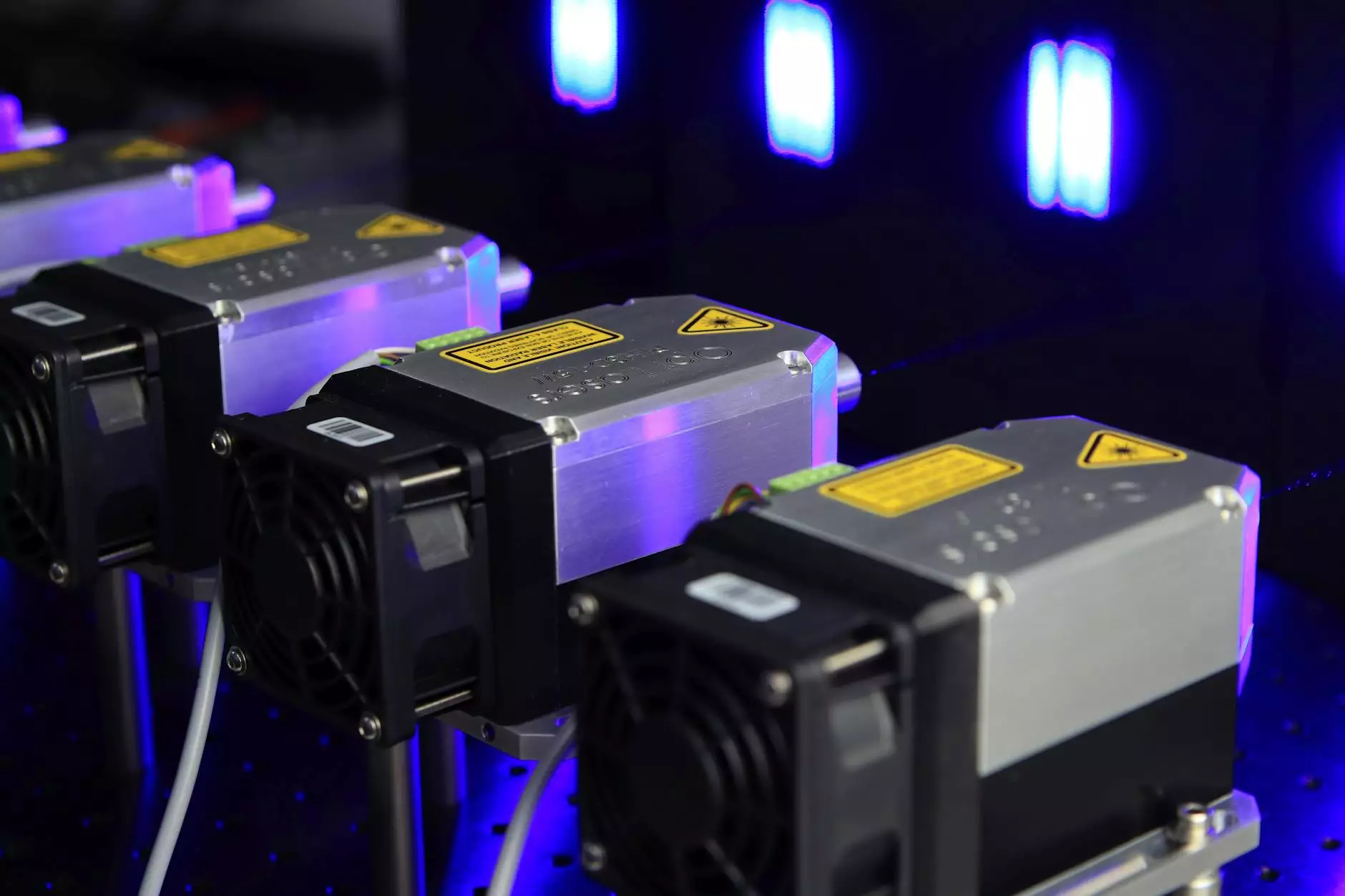
In the modern landscape of manufacturing, CNC (Computer Numerical Control) machines represent a paradigm shift in metal fabrication. Their unprecedented precision has transformed the way businesses operate, allowing for the creation of intricate designs and components that were once thought impossible to achieve with traditional methods. This article explores the remarkable capabilities of CNC machines, focusing on their precision, efficiency, and impact on the metal fabrication industry.
Understanding CNC Machines
CNC machines are automated cutting tools controlled by a computer. They follow programmed instructions to execute detailed designs accurately and consistently. The power of CNC technology allows for various processes including cutting, milling, drilling, and engraving metals with extraordinary precision. This level of accuracy makes CNC machines indispensable for industries that require high-quality components.
The Technology Behind Precision
The precision of CNC machines hinges on several key technologies:
- High-Fidelity Software: CNC machines utilize sophisticated software that converts CAD (Computer-Aided Design) drawings into machine-readable code (G-code), ensuring that the fabrication process is seamless and precise.
- Robust Hardware: The materials and components used to construct CNC machines affect their precision. High-quality linear guides, ball screws, and cutting tools ensure that the machines operate flawlessly.
- Feedback Mechanisms: Many CNC machines integrate feedback systems that provide real-time data about the machining process, allowing adjustments to enhance precision even further.
The Importance of Precision in Metal Fabrication
Precision in metal fabrication is not merely a luxury; it is a requirement. In industries such as aerospace, automotive, and medical device manufacturing, even the slightest deviation can have catastrophic consequences. Here are several reasons why precision is paramount:
1. Product Quality and Reliability
High precision ensures that components are made to exact specifications, which directly affects the quality and reliability of the final products. For example, in the aerospace industry, components must adhere to stringent tolerances to ensure safety and performance. CNC machines deliver this quality consistently.
2. Reduced Waste and Cost
By achieving higher levels of precision, CNC machines significantly reduce material waste. Traditional machining processes often result in scrap material due to inaccuracies. CNC technology minimizes this waste, thereby lowering costs and improving the overall efficiency of metal fabrication.
3. Enhanced Flexibility
The precision of CNC machines allows manufacturers to explore complex geometries and designs without the fear of compromising quality. This flexibility fosters innovation, enabling businesses to create cutting-edge products that meet market demands.
4. Faster Production Times
CNC machines operate at faster speeds compared to manual machining methods. The ability to produce precise components in a fraction of the time enhances productivity and allows businesses to meet tight deadlines without sacrificing quality.
Applications of CNC Machines in Metal Fabrication
The applications of CNC machines in metal fabrication are vast and varied. Here are some prominent uses:
- Milling: CNC milling machines are used to shape metal components with a high degree of accuracy. They can create complex parts by moving the cutting tool along multiple axes.
- Turning: CNC lathes are employed to produce cylindrical parts with smooth surfaces. They are ideal for creating shafts, bolts, and other rotational components.
- Plasma Cutting: CNC plasma cutters use high-velocity plasma to cut through metal with precision, making them suitable for large sheets of material.
- Laser Cutting: CNC laser cutting machines utilize focused laser beams to cut intricate designs into metal, ensuring a high-quality finish.
Improvements in CNC Technology
As the demand for precision in various industries continues to grow, so does the evolution of CNC technology. Recent advancements include:
1. Adaptive Machining
Adaptive machining technologies allow CNC machines to make real-time adjustments based on feedback from sensors. This leads to even greater precision and quality due to the machine's ability to correct itself during the cutting process.
2. Increased Automation
The introduction of automation technologies, such as robotic arms, has further enhanced the capabilities of CNC machines. This combination allows for uninterrupted production runs and reduced labor costs.
3. IoT Integration
With the rise of the Internet of Things (IoT), CNC machines can now be connected to the internet for remote monitoring and control. This connectivity allows manufacturers to analyze machine performance and optimize processes continuously.
Choosing the Right CNC Machining Partner
For businesses seeking to harness the precision of CNC machines, carefully selecting a machining partner is crucial. Here are some factors to consider:
- Experience: Look for a partner with extensive experience in the metal fabrication industry, particularly with CNC machining.
- Capabilities: Ensure the partner can handle the specific materials and complexities of your projects.
- Technological Advancements: Choose a partner that keeps up with the latest CNC technologies to ensure access to the most efficient processes.
- Quality Assurance: Look for companies that implement rigorous quality control measures to guarantee precision in every project.
The Future of CNC Machines in Metal Fabrication
The future of CNC machines is bright, with numerous innovations on the horizon. As technologies such as artificial intelligence and machine learning continue to develop, we can expect even greater enhancements in the precision of CNC machines. This progress is likely to redefine industry standards and challenge traditional manufacturing methods.
Conclusion
The precision of CNC machines is a game-changer in the world of metal fabrication. Their ability to produce high-quality, reliable components efficiently has revolutionized the manufacturing landscape. As industries continue to evolve, the demand for precision will only increase, and CNC technology will remain at the forefront of this transformation.
As companies like Deep Mould leverage the power of CNC machining, they position themselves not just as manufacturers, but as leaders in innovation, quality, and efficiency in the metal fabrication sector. The journey towards perfection, powered by the precision of CNC machines, is well underway.